Соляной туман: метод тестирования на коррозийную стойкость
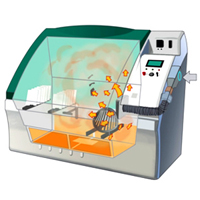
Неслучайно соль в народном эпосе считается сакральной приправой. Выражение «съесть пуд соли» означает пройти испытание годами и лучше узнать друг друга. Так и в промышленных масштабах: если новый товар устойчив к соляному туману, значит, и в меньшей степени подвержен коррозийным процессам.
Дешево и популярно
Тестирование на испытательном лабораторном оборудовании соляным туманом – это стандартный способ уточнить стойкость покрытия к коррозии. Идея использовать соль для экспериментов родилась в начале прошлого столетия. А уже к 40-м годам был разработан и опубликован первый международный стандарт для испытаний, который используется и в современных реалиях.
Тестирование проводится с 5% раствором поваренной соли, из которой получают туман. Иногда в качестве исходного реактива могут использоваться уксусная кислота или хлорид меди, который применяют для воздействия на декоративные поверхности.
Стандартизация
Любопытным является тот факт, что нет единого стандарта, который бы описывал допустимые параметры коррозии. В каждом конкретном случае производитель согласует с потребителем условия проявления ржавчины. Лишь затем предоставляются данные, выражаемые в часах пребывания в камере соляного тумана до появления белых следов разрушения.
Оборудование
Устройство для тестирования представляет собой герметичную камеру, куда заливают соляной раствор. Чтобы результат оказался достоверным, требуется цикличное проведение испытаний в определенной последовательности.
- На первой фазе формируется солевой туман, а также создаются условия для испытаний.
- Затем происходит сушка изделий в температурном диапазоне, приближенном к естественной среде. Иногда требуется провести дополнительный влажный контроль воздуха. По завершении 2 этапа материалы в камере должны остаться сухими.
- После сушки воздухом температуру и влажность вновь повышают до образования конденсата, который выпадает на тестируемый объект.
- А затем выставляются параметры, которые будут сопровождать стадию контроля влажности.
Перечисленные этапы не раскрывают сути испытания, а лишь дают представление в общих чертах. Поэтому для испытаний нередко используется оборудование, которое создается по индивидуальному проекту или требует доработки уже имеющихся моделей.
О достоинствах
К плюсам такого тестирования относят создание условий, приближенных к реальным, что позволяет получить точный прогноз об эксплуатации транспортных средств и иных объектов.